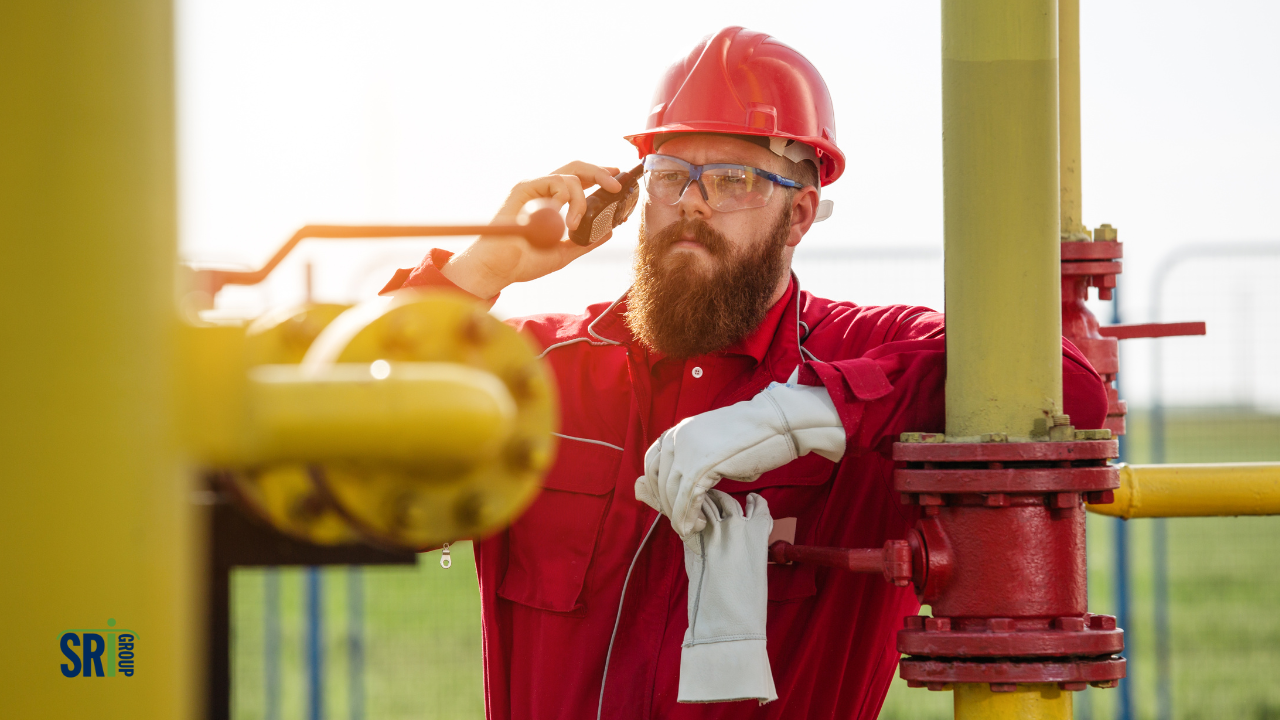
How SRI’s Approach to Contractor Safety Programs Saves Lives
Two years ago, I attended a presentation given by a mid-sized industrial contractor which overviewed their new event management system. At the end of the presentation, the leader of their group asked for volunteers to participate in an industry focus group related to contractor safety. He cited statistics showing the decline in TRIR, but also showing a rise in contractor fatalities. Beginning in 2011 through 2016, Contractor TRIR has been reduced by roughly ten percent. While the number of contractor fatalities and the fatality rate has risen by more than fifty percent.
“Despite advancements in contractor safety, many still lose their lives in workplace incidents. Let’s explore the evolution, progress, remaining challenges, and solutions for better safety.”
I began my career with The SRI Group in the mid-1970s. At that time, there were those who believed in a “hands off” approach to contractor safety. Others believed in a limited “hands on” approach and still others who advocated active involvement. Common attitudes and practices for many companies at that time are listed below.
- There existed a prevailing attitude that contractor safety was the responsibility of the contractor and that any attempt to interfere or set requirements might bridge co-employment barriers and increase the liability of the company (hiring client).
- Prequalification and vetting of safety programming was often limited to a review of required insurance and fiscal soundness.
- Contractor safety programming consisted of little more than tailgate meetings, job site inspections and conducting most required regulatory training.
- Enforcement of rules and procedures was the contractor’s responsibility, but the hiring client did expect its own safety professionals to “catch” contractors violating rules and procedures. These safety professionals could usually remove the individual contractor employee from the location, but they had very limited power to remove the contractor company.
Our History with Contractors
At SRI, we’ve partnered with numerous clients who’ve recognized the inefficacy of traditional contractor safety methods. They’ve embraced our proactive approach, which has demonstrably lowered incidents, liabilities, and expenses. This method, honed over three decades, has saved countless lives and potentially billions of dollars. This comprehensive approach encompasses:
- Rigorous assessment of each contractor’s safety program during the bidding phase.
- Setting maximum tolerable levels for Total Recordable Incident Rate (TRIR) and Experience Modification Rate (EMR), beyond which no contractor can win the bid.
- Initiatives to enhance the contractors’ grasp of the client’s safety prerequisites.
- Considerable augmentation in the orientation training for all contractor staff and subcontractors.
- Requiring every winning contractor to present an approved safety action plan, which includes:
- All-staff orientation.
- Adherence to housekeeping standards.
- Job site inspections.
- “Tailgate” meetings at the commencement of each shift.
- Regular safety gatherings.
- Continuous regulatory compliance training.
- Safety coaching and observations.
- Task analysis, incident investigations, and emergency response training.
- “What-if” drills.
- Industrial health and hygiene measures.
Contractors were expected to implement safety programs aligning with the hiring client’s protocols. Additionally, contractors working closely with the client’s staff were expected to fully participate in the client’s safety protocols.
Those accountable for the project’s timely completion and budget adherence were also responsible for the contractors they supervise, ensuring compliance with rules and the safety action plan. Strict enforcement of client rules was mandatory, with the understanding that removing an individual contractor for violations was insufficient. The emphasis was on guaranteeing the contracting company’s compliance with all rules and the execution of the safety plan. Failures resulted in the contractor’s removal from the premises and the approved bidder’s list.
By adopting these fundamentals, we’ve seen a drastic reduction in contractor injuries and virtually zero fatalities. Unfortunately, not all private companies utilize these practices, and their adoption in the public sector is extremely sparse. Many public entities, under the illusion of limited liability, have substandard contractor safety efforts compared to even the weakest private sector practices.
Mitigating Factors
Unintended Consequences
The second wave of significant advancements began roughly twenty years ago and included a number of activities which were highly valuable, but which often had unintended consequences. Contractor prequalification companies were established to relieve hiring clients from the burden of vetting all of the bidding contractors. These companies evaluate contractor worthiness on criteria chosen by the hiring client and then provide that data to the hiring client for consideration in the award of the bid.
Most of these services are remarkably similar. Services rendered usually include:
- Review of liability and other required insurance
- Review of LDAR, TRIR, and EMR rates
- Confirmation of required certifications and training
- Auditing the contractor’s written safety procedures
- Some limited evaluation of safety programming
The Downside
The time and money saved by hiring clients was substantial and the fee charged to the contractors was minimal. Hiring clients could, at a glance, see which contractors meet their requirements. The downside to these services was:
- They are backward looking with regard to injury rates, EMR, etc.
- Contractors who did not have the necessary programming could simply purchase it from various providers creating the illusion that their written safety programs met the requirements.
- Much of what is evaluated is irrelevant in continuous process industries, as the contractor will be expected to work under the hiring client’s procedures.
In larger metropolitan areas, local safety councils prevent began to provide contractor orientation services. Hiring clients would convey their orientation requirements. The safety council will then conduct orientation training with the contractor. This relieved some of the hiring client’s internal costs, but it also provided a less comprehensive window regarding the knowledge and skills of the employees coming to their site.
Another practice which gained acceptance amongst some hiring clients was the inclusion of contractor incidents and the data provided for the site to the corporate parent. Some even went as far as to link both the incidents of company’s personnel and contractor in calculations for goals, bonuses, and other remuneration for site leadership. This practice has led to unintended yet proven predictable consequences, extreme levels of injury management, along with outright underreporting of contractor incidents.
Challenges to the Current Landscape
- Contractors battling stiff competition with shrinking profit margins.
- A rising number of non-English speaking contractors.
- A lack of skilled craftsmen.
- A shift in vocational education towards medical, IT, and service sectors, reducing the number of trainees in manufacturing jobs.
Given these challenges, it’s easy to feel overwhelmed, but effective solutions are available.
The SRI Approach to Contractor Safety
- Conduct extensive evaluations through their prequalification providers.
- Enforce site-specific orientation by their personnel in addition to the contractor’s basic orientation.
- Require contractors to present a comprehensive safety action plan, holding them accountable for its execution.
- Involve resident and supplemental contractors more comprehensively in their safety efforts.
- Hold personnel responsible for project success accountable for contractor safety outcomes and their safety action plan’s implementation.
- Ensure that contractors are aware that non-compliance with safety protocols or rules will lead to their removal from the site and the client’s approved vendor list.
The SRI Group’s innovative TIPPS 3 safety software allows clients to view contractor safety programs in real-time. This tool tracks each contractor’s safety action plan, archives preventive activities, and generates trend data for insightful safety analysis. In essence, TIPPS 3 offers clients unparalleled transparency and facilitates accountability.
It’s crucial for clients to continue forming partnerships with proven contractors, fostering an environment of mutual trust that benefits both parties. Accountability should be maintained at all levels, within both the client and contractor teams.
Contractors need to understand that simply meeting minimal client expectations isn’t enough. In the future, contractors offering value-added services and effective management systems will be favored over those who don’t.
Clients should also actively engage with local communities and vocational schools to help shape tomorrow’s workforce. This includes imparting basic workplace safety knowledge and legal practices to students.
By eschewing short-term thinking, adopting innovative technologies for improvement, and implementing proven fundamental systems, hiring clients and contractors can save many lives in the process.
If you would like to learn more about The SRI Group or TIPPS 3 Safety Software Contact SRI Today