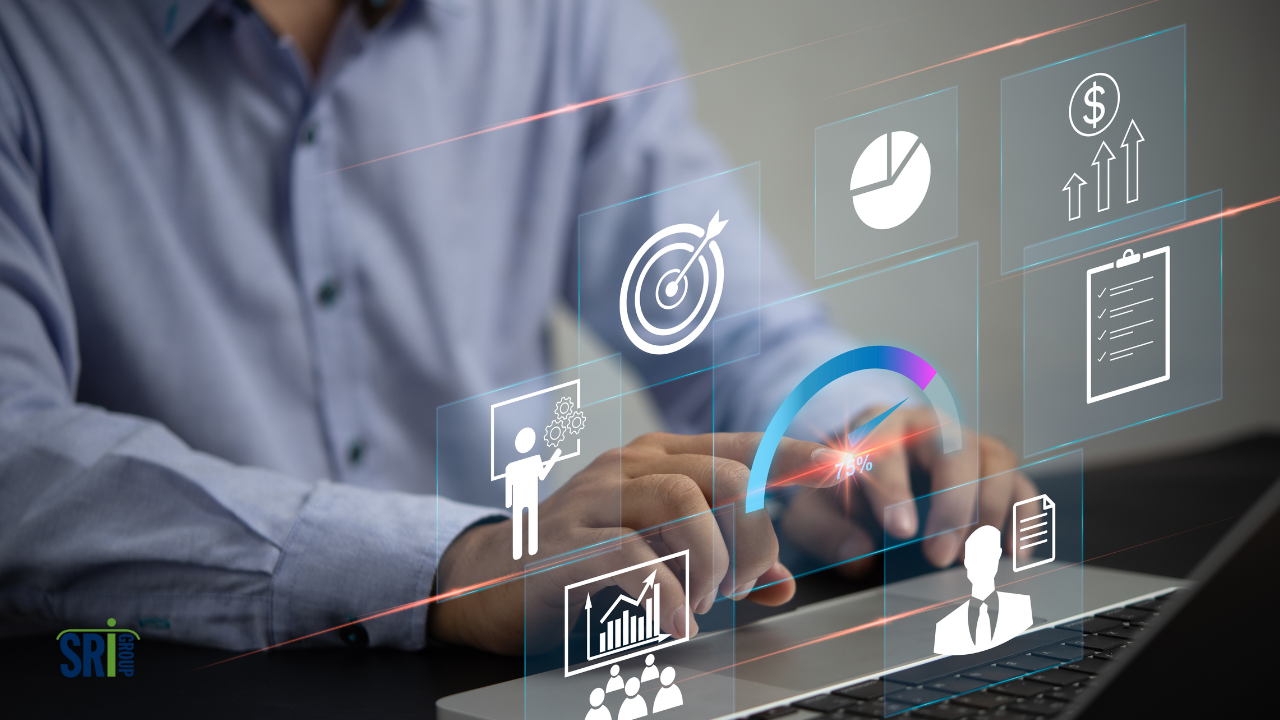
Measure What Matters – Safety KPIs
Fifteen years ago, I sat in on a Chemicals Business Unit Leadership Team meeting in a large integrated oil company. The meeting revolved around the Process Safety Metrics introduced by the new CEO. “These must have come from the Refining group” complained one participant. He continued, “the new CEO doesn’t understand chemicals.” The exact same conversation was happening within all the other Business Units. In fact, the new CEO had simply imposed the same metrics from his previous company not knowing they would cause such a stir. Different company, different culture, different status of maturity; it’s not surprising these measurements caused such consternation. Over the next year employees from each Business Unit spent countless hours collecting and processing what they perceived as “worthless data.” With no agreement on the validity of the measurement is it any wonder there was at best a halfhearted effort to use this data to identify issues and plan improvement?
Measurement is easy. Measuring the right things is hard and using effective measurement to move the needle is even harder. Here we will review what The SRI Group (SRI) and our clients have learned about meaningful measurement. 40 plus years with some of the finest companies throughout the world have given SRI some insights as to the “what,” “where,” “when,” and “who” of measuring the right things.
The Basics of Measurement
Bill Brenneman once said, “outcomes are a result of process,” and this principle rings true. Results aren’t the product of chance, magic, or wishful thinking. They arise from meticulously designed systems and processes. For over two decades, my father advised clients, “focus on the process, and the results will take care of themselves.” He acknowledged that while results matter, improved results could only be achieved through process enhancement.
Martin Ferris, another thought leader in this field, taught us that “measurement is first a social process.” This means if the participants in a process don’t understand or agree with the measurement’s premise, there won’t be a consensus on results or motivation to use the data for improvement. Tom Tarwater helped us learn the mechanics of process measurement, a topic we will explore further in this paper.
Over the past 30 years, there’s been a lot of debate around “reactive” versus “proactive” metrics. All metrics measure what has happened or what is currently happening. Using data for prediction, analysis, and forecasting is proactive and can guide real improvements, but only under these conditions:
- A process is established.
- There’s agreement on how to measure process elements and sub-elements.
- A tool is available to evaluate data from activities and systems.
- There’s a requirement to develop improvement plans using the data.
Our Structured Safety Process™ (SSP) is one of the most effective safety improvement initiatives to date. It has helped thousands of clients achieve and sustain top-tier performance, primarily because SSP measures all critical elements, then uses that data for immediate improvement planning. It measures activities and inputs, processes and systems, compliance and effectiveness, and results.
With our Total Incident Prevention & Planning (TIPPS3™) software, clients can measure individual participation, the quantity and quality of prevention activities, and the completion of assigned responsibilities. This approach enhances personal accountability and allows for recognizing safety champions.
SSP, leveraging TIPPS3, collects data from numerous prevention activities:
- Peer-to-Peer Observations
- Task Assurance/Competency Observations
- Permit Audits
- Safety Inspections
- Manager’s Assessments
- Human Reliability Observations
- And many more
Each team (comprising supervisors and employees) uses data from these prevention activities to develop custom action plans. These plans eliminate the errors causing incidents and losses. Every workgroup analyses their data, then plans strategies to eliminate risky behaviors and substandard conditions. This active involvement in data usage and performance improvement planning isn’t because they can’t—it’s likely because they haven’t been asked or equipped to do so. Tools like TIPPS3™ can empower them. SSP also requires Improvement Plans at the area and department levels, which TIPPS3™ can facilitate.
Measuring Process / Systems / Compliance
Assessing activities and results is a straightforward task. However, evaluating processes and systems presents a more challenging and intricate endeavor. To effectively tackle this, several elements are required:
- A clear, written process should be established.
- All elements and sub-elements of the process must be well-defined.
- Defined prerequisites for the implementation, execution, and enhancement of each sub-element should be in place.
- Agreed metrics for each sub-element are essential.
- There should be a systematic method to assess and review processes.
- These metrics should be utilized to identify gaps and formulate improvement plans.
We witnessed a remarkable example of this with one of our clients, who made tremendous strides in safety performance, earning them the industry leader title for two consecutive years. While their results exceeded expectations, there were inconsistencies at different site locations. They sought our assistance to create a tool capable of measuring process implementation and execution. In response, we developed the eMAP™ Software.
eMAP™ is an online management system assessment tool. We utilized our client’s HES Management System (HESMS) criteria as the foundation for assessment. We then collaborated with them to determine the evaluation factors that would be employed to assess each element and sub-element. Alongside client personnel, SRI conducted the initial baseline assessment at all six facilities. This was then supplemented by self-assessments completed by each facility and assurance assessments by Corporate HES.
The initial results are promising. Facilities that scored the highest in implementing and executing the HESMS have the lowest Total Recordable Incident Rate (TRIR), while those with the lowest scores have the highest TRIR. Over the past five years, the facilities with the lowest evaluation scores – and correspondingly high TRIR – have utilized data-driven action plans to fill gaps in HESMS execution, bringing them in line with the higher-performing facilities. This success pattern has been replicated with numerous clients.
Measuring Results
Evaluating results such as the Recordable Incident Rate or Lost Work Day Rate is relatively straightforward; the government provides clear definitions and formulas for calculation. Since the start of my career, the overall Recordable Incident Rates have been halved. Workplace fatalities have also dropped from around 7,500 annually to approximately 5,200, a reduction of nearly 30%. However, both the number and rate of fatalities per 100,000 employees have remained stable for almost a decade.
What’s concerning is the shift in the ratio of Recordables to Fatalities. Forty years ago, this was at 1,175 Recordables for each fatality. Now, even with more stringent criteria for what constitutes a Recordable, we’re at 563 Recordables for each fatality – half of what it used to be. This shift is primarily due to aggressive “Injury Management,” under-reporting of minor Recordable incidents, and the use of Total Recordable Incident Rate (TRIR) as a factor in performance appraisals.
For the past four decades, we’ve advocated for our clients to measure individual or group performance using a blend of task completion, implementation and execution of core processes, and final results. While many executives have taken on this advice, adding “results matter,” it’s crucial to remember that results are a product of the process. Overemphasis on results, especially when tied to compensation, can encourage under-reporting and sometimes even manipulation of data.
This same principle applies to contractors in manufacturing and construction. When overly ambitious TRIR targets can affect work contracts, some contractors may provide whatever rates necessary to secure the job. We’ve found it’s much more effective to evaluate the contractor’s safety management system and adherence to their Safety Action Plan provided to hiring clients, rather than relying solely on incident rates. To facilitate this, we’ve developed TIPPS3. TIPPS3 empowers hiring clients to efficiently review contractor’s adherence to the preventive activities outlined in the agreed-upon Safety Action Plan.
Conclusion
Effective measurement requires structured systems, agreed upon metrics and the tools and technology to measure effectively and quickly. It also requires the engagement of all personnel within the organization and their ability to evaluate data and then develop plans for gap closure and improvement. Many of our clients have learned these lessons, made these investments and have created some of the finest records in the history of industrial safety.